Clever Workshop Organization Ideas That Save Time
You’ll save significant time by implementing strategic workshop zones that separate cutting, assembly, and finishing areas to reduce daily movement by up to 805 meters. Start with decluttering tools into “necessary” and “unnecessary” categories, then install pegboards to free 30% of floor space and magnetic strips for quick metal tool access. Use color-coded containers and mobile carts to bring tools directly to workstations, eliminating back-and-forth trips. These foundational strategies reveal even greater efficiency opportunities.
We are supported by our audience. When you purchase through links on our site, we may earn an affiliate commission, at no extra cost for you. Learn more. Last update on 22nd August 2025 / Images from Amazon Product Advertising API.
Notable Insights
- Create distinct zones for cutting, assembly, finishing, and storage to minimize transport time and reduce daily movement by up to 805 meters.
- Use pegboards with customizable hooks and magnetic strips to exploit vertical wall space, freeing up 30% of floor area for workflow.
- Implement mobile carts with multi-tier shelving to bring tools directly to workstations, eliminating back-and-forth trips during projects.
- Categorize tools by frequency of use with color-coded containers and clear labels to reduce search time and improve accessibility.
- Install automated tool dispensing systems and workflow management software to track usage and coordinate projects more efficiently.
Declutter and Categorize Your Tools and Materials
The foundation of workshop efficiency begins with a systematic approach to decluttering and categorizing your tools and materials.
Start your tool inventory by creating distinct zones labeled “Necessary” and “Unnecessary.” Ask yourself if each item supports current or planned projects. Remove broken, redundant, or rarely used tools immediately.
Effective sorting requires categorizing items by frequency and function. Group tools into daily, weekly, and rarely used categories. Place frequently accessed items in prime locations within arm’s reach. Store seldom-used equipment in less accessible areas. This decluttering process helps minimize distractions by creating a more focused work environment.
Use standardized containers with clear labels for each category. Label containers for small items like screws to maintain precise organization and prevent loss of essential hardware.
Color coding enhances visual organization and reduces search time by up to 30%. Group similar tools together for intuitive placement.
This systematic approach creates workflow efficiency while preventing accumulation of outdated duplicates.
Design Strategic Workshop Zones for Maximum Efficiency
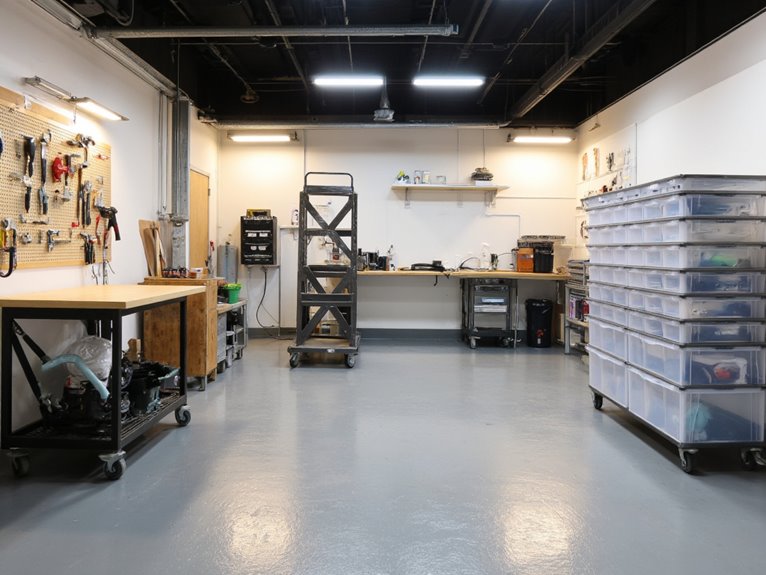
Strategic workshop zones function like assembly lines in manufacturing facilities, where each designated area serves a specific purpose within your overall workflow.
You’ll need to separate your workspace into distinct zones: cutting, assembly, finishing, storage, and quality control. Each zone requires task-specific tools and adequate space to prevent crowding.
Workflow mapping determines ideal zone placement. Position frequently used areas like cutting and material storage adjacent to minimize transport time. Studies show proper layouts can reduce movement distance by up to 805 meters daily. Task allocation becomes more efficient when you place interdependent processes closer together.
Strategic zone placement cuts daily movement by hundreds of meters, boosting efficiency when interdependent processes work in proximity.
Design finishing zones with dedicated ventilation systems for safety. Create flexible, multi-use areas with movable workstations to accommodate varying project sizes. Implementing ergonomic principles in each zone reduces physical strain and enhances worker comfort throughout extended projects.
This systematic approach reduces labor effort while increasing throughput. Proper organization also protects your tool investment by providing designated storage areas that prevent damage from mishandling or environmental exposure. Consider incorporating portable cooling solutions like mini coolers in break areas to maintain comfort during extended workshop sessions.
Invest in Smart Storage Solutions That Work
You’ll need storage solutions that adapt to your specific tools and workflow requirements rather than forcing your equipment into generic containers.
Smart storage systems like pegboards with customizable hook arrangements, magnetic strips for metal tools, and mobile carts provide the flexibility to reconfigure your setup as projects change.
Modular shelving systems offer the most versatility, allowing you to adjust shelf heights and compartment sizes while maximizing your workshop’s vertical space efficiency.
Pegboards and Magnetic Strips
Two fundamental storage solutions can transform any cluttered workshop into an organized workspace: pegboards and magnetic strips.
Pegboards exploit vertical wall space up to nearly full height, freeing approximately 30% of floor area compared to traditional storage methods. You’ll reduce tool retrieval time considerably when everything remains visible and accessible.
Pegboard accessories like bins, shelves, and specialized hooks extend functionality beyond basic tool hanging. Wood, metal, and plastic options accommodate different weight requirements and workshop aesthetics.
Magnetic tool storage complements pegboards by securing metal items without consuming additional space. This combination centralizes hand tools, power tools, and small components in one reachable area.
You can reconfigure layouts quickly as projects evolve without time-consuming overhauls. Quality hardboard and metal pegboards withstand heavy loads for years while providing excellent long-term value.
Mobile Cart Solutions
While pegboards maximize vertical storage, mobile carts bring your tools directly to each workstation without the constant back-and-forth trips that waste productive time.
You’ll reduce tool retrieval time by 25% when everything rolls with you.
Modern carts feature multi-tier shelving systems with locking mechanisms and adjustable compartments. Swivel casters with integrated braking systems provide superior maneuverability in tight spaces.
Mobile cart customization includes removable bins, accessory mounts, and modular configurations that adapt to specific workflow requirements.
Ergonomic features reduce user fatigue through optimized handle heights and weight distribution.
Digital configurators let you visualize storage layouts before purchase, ensuring maximum efficiency.
These solutions support lean manufacturing principles by eliminating wasted motion.
Investment costs average $200-800 per unit but deliver measurable productivity gains through streamlined tool access and improved workspace organization.
Modular Shelving Systems
The most sophisticated workshops rely on modular shelving systems that transform chaotic storage into engineered efficiency. These units maximize vertical space utilization while maintaining floor area for active work zones.
You’ll achieve optimal shelf customization by adjusting compartment depths from 8 to 24 inches to accommodate varying tool sizes. Modular systems enable workspace reconfiguration without costly renovations.
Standard units support 150-300 pounds per shelf, depending on material specifications. Steel frameworks provide maximum durability, while powder-coated finishes resist workshop chemicals and moisture.
Your productivity increases when tools remain visible and accessible. These systems reduce search time by 40% compared to traditional storage methods.
Component-based design allows gradual expansion as needs change. You’re investing in adaptable infrastructure that grows with your workshop requirements rather than limiting future capabilities.
Enhance Safety Through Thoughtful Organization
Your workshop’s organization directly impacts safety outcomes, as poorly arranged tools and materials create hazardous conditions that can lead to serious injuries.
You must establish secure storage protocols for dangerous equipment, maintain spotless work surfaces to prevent slips and falls, and designate specific zones for chemical materials based on their compatibility and risk profiles.
These organizational strategies form the foundation of accident prevention, transforming your workspace from a potential liability into a controlled environment where safety protocols function effectively.
Secure Hazardous Tool Storage
Every workshop contains tools that pose significant injury risks, making secure storage systems absolutely critical for protecting both workers and equipment.
You’ll need lockable cabinets or tool chests to restrict unauthorized access to hazardous tools like cutting implements and power equipment. Separate these dangerous items from general tools using designated storage areas with clear safety markings.
Implement check-out systems to track tool usage and guarantee timely returns. Store cutting tools with blade guards in dedicated compartments—never in loose boxes or pockets.
Wall-mounted pegboards maximize space while improving visibility. Maintain dry storage conditions to prevent corrosion that causes tool malfunction. Label each storage unit with safety information and inspection dates.
Use color-coded containers for quick hazard level identification, keeping frequently used items accessible without creating clutter.
Prevent Accidents With Cleanliness
Thirty-five percent of all workplace injuries stem from slips, trips, and falls—making cleanliness your most powerful weapon against workshop accidents.
Poor housekeeping contributes to 40% of workplace falls, yet implementing regular cleaning routines reduces accidents by approximately 30%.
Establish clear cleaning responsibilities for specific areas and frequencies.
Foster a “clean-as-you-go” mindset throughout each workday to prevent hazard accumulation.
Schedule weekly walkthroughs using structured checklists that identify trip hazards, blocked pathways, and improper waste disposal.
Maintain clear aisles and emergency exits at all times.
Mark walkways with visible tape to reinforce boundaries and prevent obstruction-related incidents.
Workplace hygiene directly impacts injury prevention.
Clean workshops boost productivity by 15% while enhancing job satisfaction by 20%.
Daily cleaning schedules prevent hazard buildup and maintain efficient workspaces.
Proper Chemical Material Placement
While cleanliness prevents slips and falls, improper chemical storage creates far more severe hazards including fires, toxic exposures, and environmental contamination. Effective chemical organization requires strict adherence to placement guidelines and safety compliance protocols.
Never store liquid chemicals above shoulder height to prevent handling accidents. Store flammable liquids in designated cabinets, limiting outside storage to 10 gallons maximum.
Segregate incompatible materials—oxidizers separate from phenols, cyanides away from acids. Secondary containment becomes mandatory when volumes exceed 55 gallons individually or 100 gallons aggregate.
Essential chemical storage requirements:
- Install spill sump systems with minimum four-inch depth for leak containment
- Restrict access to authorized personnel only with clear labeling
- Group chemicals by hazard class and reactivity for ideal safety
- Maintain readily accessible Safety Data Sheets for each stored chemical
Leverage Technology and Automation for Better Workflows
Although technology adoption accelerates across industries, many workshops still rely on outdated manual processes that drain productivity and inflate operating costs. You can reduce operating expenses by 22% through strategic automation implementation.
Digital transformation becomes achievable when you automate inventory tracking, tool management, and workflow scheduling systems.
Start with robotic process automation for repetitive tasks. RPA delivers 30-200% ROI within twelve months. Install automated tool dispensing systems that track usage patterns and maintenance schedules.
Deploy workflow management software to coordinate project timelines and resource allocation.
Over 90% of workers report productivity increases after automation adoption. You’ll eliminate manual inventory counts, reduce tool search time, and streamline project handoffs.
Focus automation efforts on tasks consuming excessive time daily. This systematic approach transforms workshop operations from reactive maintenance to proactive efficiency optimization.
Maintain Tool Longevity and Workspace Cleanliness
Proper tool maintenance and workshop cleanliness directly impact operational efficiency and equipment lifespan. Implementing systematic tool preservation strategies prevents premature wear and reduces replacement costs.
Strategic tool care and workspace organization maximize efficiency while minimizing equipment replacement expenses through systematic preservation methods.
You’ll need dedicated storage solutions like pegboards or tool chests to protect equipment from moisture and contamination.
Effective maintenance routines require immediate post-use cleaning with material-specific agents. Document all activities to track tool condition and predict replacements.
- Store tools in dry environments using silica gel packs or rust inhibitors for corrosion prevention
- Establish cleaning schedules that remove dust, grease, and residues immediately after use
- Maintain clear walkways and designated zones for storage, work areas, and waste disposal
- Control humidity levels with dehumidifiers and implement air filtration systems
Visual management systems like shadow boards guarantee proper tool return and maintain organizational discipline throughout daily operations.
Create Flexible Systems That Adapt to Your Projects
Component Type | Mobility Feature | Adaptability Benefit |
---|---|---|
Workbenches | Rolling casters | Repositions for project scale |
Tool storage | Wheeled chests | Follows workflow patterns |
Parts bins | Stackable modules | Expands with inventory needs |
Work surfaces | Fold-down design | Creates space flexibility |
Storage units | Modular sections | Reconfigures for changing projects |
Categorize tools by frequency and project type rather than rigid classifications.
On a final note
You’ve built a workshop system that works. Your tools stay organized. Your projects move faster. Your workspace stays safe. But these systems need maintenance. Check your organization monthly. Adjust storage as your tool collection grows. Update zones when your work changes. Clean regularly to prevent buildup. Replace worn labels and containers. Your workshop’s efficiency depends on consistent upkeep. Stick to these habits, and you’ll save time on every project.